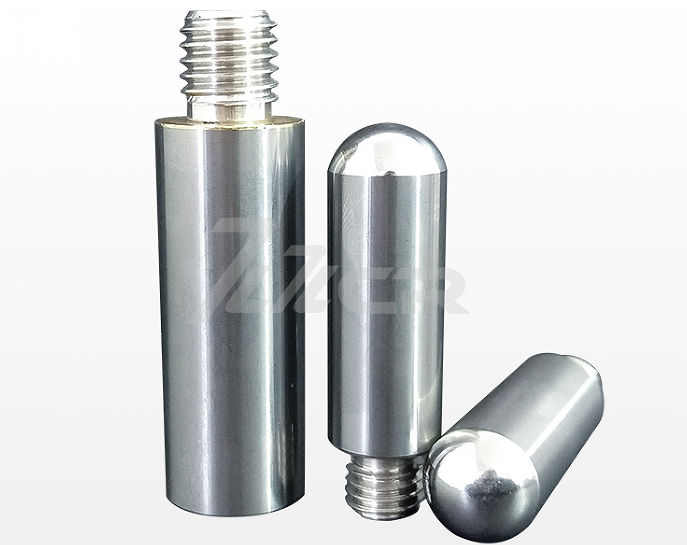
Introduction
Tungsten carbide is known as "industrial teeth" because of its high strength and hardness, as well as excellent wear resistance and corrosion resistance, and is widely used in military industry, aerospace, machining, metallurgy, oil drilling, mining tools, electronic communications, construction and other fields. Brazing of tungsten carbide is one of the effective ways to firmly join the carbide and steel body together. However, in the process of use, we often have the phenomenon of desoldering in brazing.
Reasons
When analyzing the reasons why cemented carbide is brazed, we can investigate the brazing agent, brazing metal, brazing process, etc.:
1, First of all, the strength of the solder used in brazing is not strong enough to meet the working standard or the wettability of the brazing metal to the cemented carbide is poor, and the cemented carbide tool will be directly desoldered. Therefore, we must remember not to use brazing metal or brass or miscellaneous copper as solder without calculation or verification.
2, Secondly, when the brazing agent with poor activity is used, the deoxidation effect of the brazing agent is weak, and the effect of reducing the surface tension of the liquid brazing metal is also relatively weak, the brazing material can not wet the brazing surface of the workpiece well, the brazing welding rate is low, and the cemented carbide tool is prone to desoldering. In addition, the melting temperature of the brazing agent does not match the melting temperature of the brazing metal, and it cannot play a good role in deoxidation. Therefore, the choice of flux is very important when brazing carbide tools.
3, Third, if the heating temperature is too high during brazing, the brazing metal will produce oxidation and porosity, the heating temperature is too low, the brazing seam will not be welded through or slag inclusion, too high and too low temperature will lead to desoldering, the brazing temperature is best controlled above the liquid phase of the brazing metal 30~50 °C. In addition, cemented carbide should be preheated during brazing to eliminate porosity and slag inclusions to make the welding full!
4, Finally, the tungsten carbide brazing surface is not sandblasted or polished before brazing, and the oxide layer on the tungsten carbide brazing surface will affect the wetting of the solder and affect the strength of the brazing joint. Therefore, the tungsten carbide tool should first clean the welding surface when welding.
Due to the different composition of various grades of cemented carbide, their uses and brazing characteristics are different. Therefore, we also need to know more about the properties of cemented carbide, its uses and the characteristics of its brazing. When the strength of the carbide is higher, the less likely it is to produce cracks during brazing, and conversely, brazing cracks are more likely to occur. However, the hardness of cemented carbide is inversely proportional to its strength, so when we use cemented carbide, we should combine our actual needs and processing environment, and choose the right cemented carbide grade to avoid desoldering.
Zhuzhou Chuangrui Cemented Carbide Co., Ltd. has been focusing on the research and development, production, processing and application of cemented carbide for more than 15 years, we are able to combine our own experience to provide customers with professional field guidance experience in cemented carbide welding. ZZCR carbide is willing to go all out to develop together with partners.
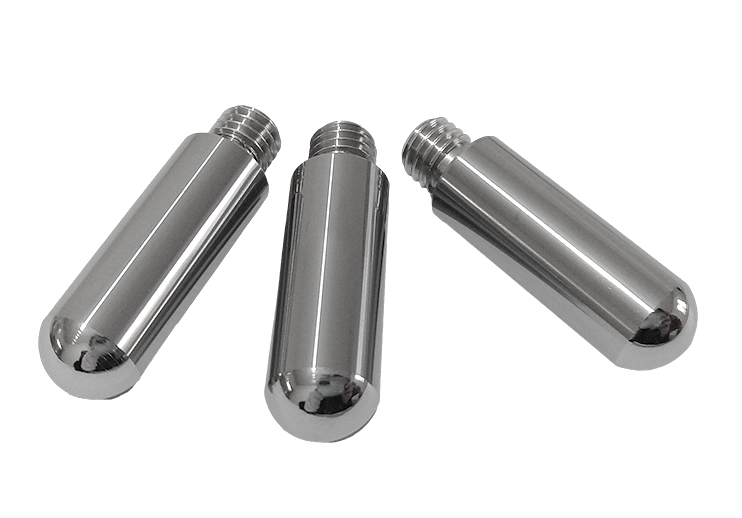
Post time: Apr-08-2025