Tungsten carbide wear-resistant parts cover a wide range, mainly including cemented carbide roller rings used in steel and other industries, top hammers and pressure cylinders for synthetic diamond, precision forming molds, precision optical molds, stamping dies, drawing dies, sealing rings, pistons, bearing journals, and surface hardening inlay welding and spraying materials. Because of the strong wear resistance of cemented carbide, these parts also have super wear resistance. However, the use environment of these tungsten carbide wear-resistant parts requires their wear resistance to continue to improve, let's take a look at how cemented carbide wear-resistant parts can improve wear resistance.


Tungsten carbide has excellent comprehensive properties such as high strength, high hardness, high elastic modulus, high toughness and high wear resistance. It is widely used in mining and oil extraction tools, molds, wear-resistant parts, and other fields that require high wear resistance. The wear properties of tungsten carbide are affected by factors such as the environment in which it is used and the properties of the alloy. The wear resistance of tungsten carbide wear parts is mainly determined by the microstructure and chemical composition of the alloy. The main structural parameters of cemented carbide are: grain size and binder phase content. The wear resistance of tungsten carbide wear parts is also affected by added elements such as boron.
In the development of modern science and technology and industrial production, many important mechanical equipment and its mechanical parts are under harsh working conditions, such as high speed, high temperature, high pressure, heavy load, etc., so the damage of mechanical parts due to wear, corrosion, oxidation, etc. often occurs. The damage of steel caused by friction and wear mostly starts from the surface. The use of surface protection measures to delay and control the damage of the surface has become an effective way to solve the wear problem of cemented carbide wear-resistant parts. Therefore, various anti-wear technologies for the surface of mechanical parts have emerged, such as plating, hot spraying, carburizing, nitriding, metallization, thermal spraying, surfacing welding, coating (physical and chemical vapor deposition, ion plating), pasting hardening layer, high-energy beam (laser or electron beam deposition, ion implantation), etc. Rare earths have been successfully applied in cemented carbide wear-resistant parts, which not only increases the alloy strength and impact toughness by more than 10%, but also improves the wear resistance of cemented carbide wear-resistant parts.
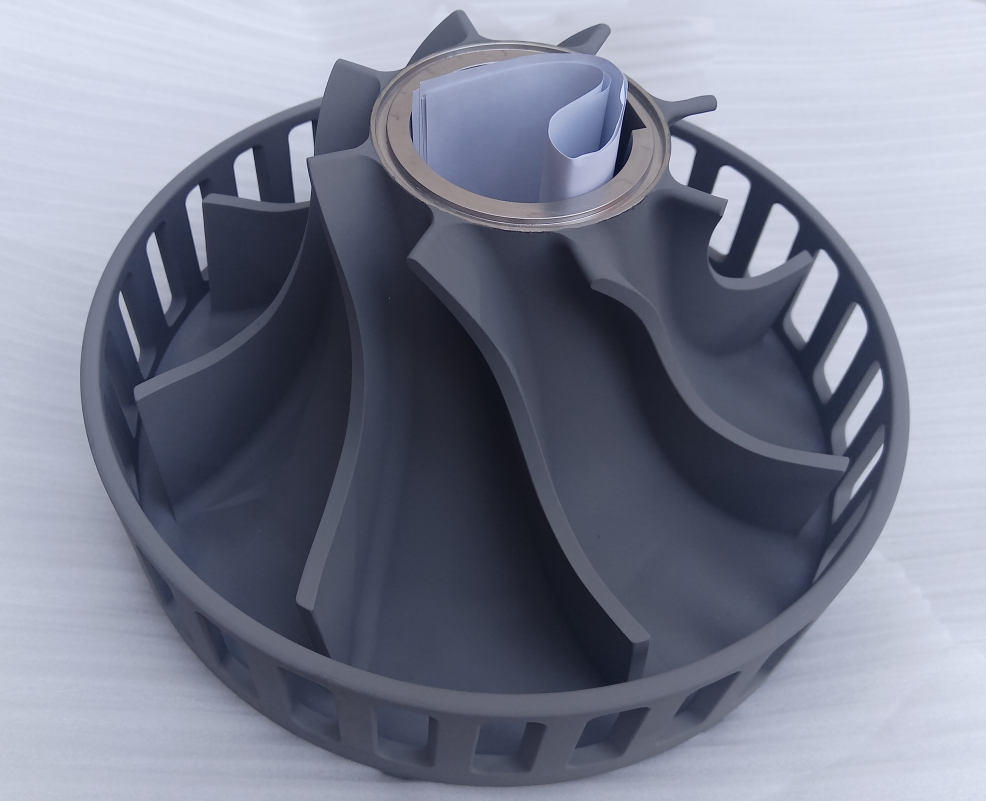
The surface protection of cemented carbide parts to control surface damage is the most effective way to solve the wear problem of cemented carbide wear-resistant parts, Zhuzhou Chuangrui cemented carbide has a variety of surface strengthening technologies, such as plasma surfacing welding, supersonic spraying, gas shielded welding, vacuum cladding, etc., which can better protect cemented carbide wear-resistant parts and prolong their service life.
Post time: May-07-2024