Tungsten carbide strip is mainly made of WC tungsten carbide and Co cobalt powder mixed by metallurgical method by pulverization, ball milling, pressing and sintering, the main alloy components are WC and Co, the content of WC and Co in different uses of tungsten carbide strip is not the same, and the use range is very wide.
One of the most materials of tungsten carbide strips, it is named because of its rectangular shape of plates (or squares), also known as tungsten carbide strip/plates. Tungsten carbide strip has excellent hardness, good wear resistance, high elastic modulus, high compressive strength, good chemical stability (acid, alkali, high temperature oxidation resistance), low impact toughness, low expansion coefficient, thermal and electrical conductivity similar to iron and its alloys.
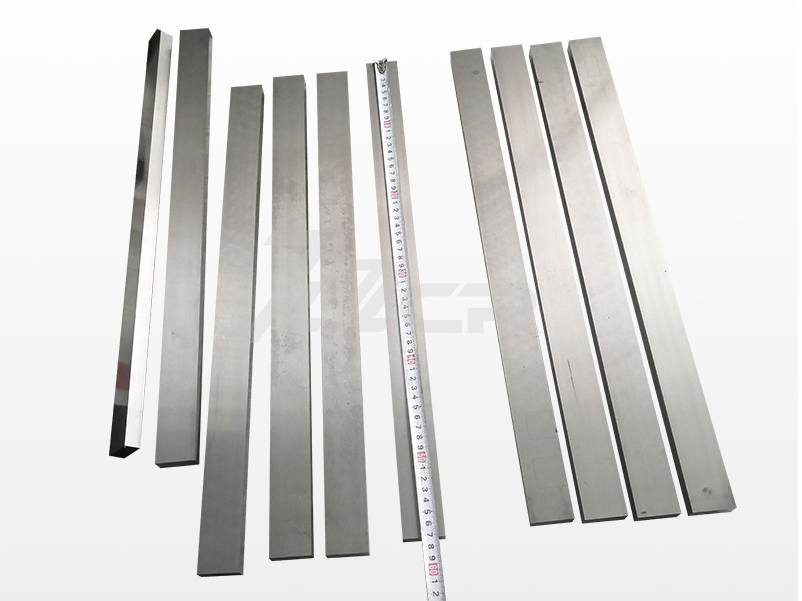
What are the reasons for the desoldering of tungsten carbide strips? Chuangrui carbide will answer next:
(1) The brazing surface of tungsten carbide is not sanded or polished before welding, and the oxide layer on the brazing surface reduces the wetting effect of the brazing metal and weakens the bonding strength of the weld.
(2) Desoldering will also occur when the brazing agent is not selected and used improperly, for example, when borax is used as the brazing agent, the borax cannot effectively play a deoxidizing role because the borax contains more moisture, and the brazing material can not be well wetted on the brazed surface, and the desoldering phenomenon occurs.
(3) The correct brazing temperature should be 30~50 °C above the melting point of the brazing metal, and desoldering will occur if the temperature is too high or too low. Heating too much can cause oxidation in the weld. Using zinc-containing brazing metal will give the weld a blue or white color. When the brazing temperature is too low, a relatively thick weld will be formed, and the inside of the weld will be covered with porosity and slag inclusions. The above two conditions will reduce the strength of the weld, and it is easy to deweld when sharpened or used.
(4)In the brazing process, there is no timely slag discharge or insufficient slag discharge, so that a large amount of brazing agent slag remains in the weld, which reduces the strength of the weld and causes desoldering.
Post time: Aug-28-2024