For cemented carbide composite products, welding is a commonly used processing procedure, but often a little careless, it is easy to produce welding cracks, causing the product to be scrapped, and all the previous processing will fall short. Therefore, it is very important to understand the causes of cracks in cemented carbide welding and to avoid welding cracks. Today, the editor of Chuangrui Technology will talk to you about the reasons for the cracks in carbide welding, and give you some reference.
In welding, different materials will have different welding characteristics. Only by knowing the type of materials to be welded can we correctly formulate the welding construction plan, so as to select the correct process standard to ensure the welding quality. The reasons for cracks in cemented carbide welding are mainly analyzed from the following factors.
First, it is determined by the characteristics of the cemented carbide Cai Laoda. As we all know, the hardness of the welding base metal depends on the carbon element in the material. With the increase of carbon content, the hardness will increase accordingly, and of course the tendency of cracks generated during welding will also increase. Therefore, cemented carbide welding is prone to cracks.
Second, when cemented carbide is welded, compared with low carbon steel, its welding heat affected zone is prone to hardened structure, which is more sensitive to the hydrogen element in welding, and the welded joint of cemented carbide can withstand greater Under stress, various cracks are prone to occur. Under the welding heat cycle, the microstructure and properties of the heat affected zone of the weld change, thereby increasing the tendency of crack generation.
Third, the embrittlement of the overheated structure in the heat affected zone of the welded joint leads to the occurrence of welding cracks. This mainly depends on the cemented carbide wood composition and the welding heat cycle, which will be affected by the high temperature residence time and cooling rate of the molten pool during welding.
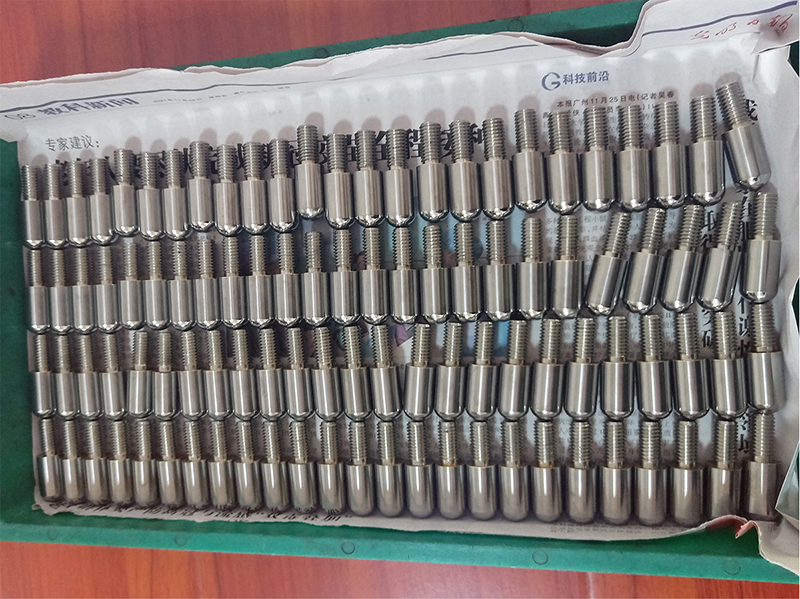
The above are several reasons why cemented carbide welding will cause cracks. For the welding of such materials, it is necessary to combine the welding characteristics of the materials to correctly select the welding materials, make preparations before and after welding, strictly abide by the process standards, and strengthen the welding process. Preheating, post-weld heat preservation and heat treatment are necessary to prevent the occurrence of cemented carbide welding cracks.
Cemented carbide is very hard and brittle. A slight negligence in the welding process will lead to scrapping due to cracks. Therefore, we must make comprehensive preparations when welding cemented carbide. Process standards to avoid welding cracks.
Post time: May-31-2023