The chemical industry is an industry with a harsh environment, equipment such as pipelines and valves play an important role in the modern chemical industry. Valves are challenged by harsh environments in conveying pipelines such as powders, granules, and slurries, and are often prone to valve pipe wear and failure. Therefore, we need to use a strong wear-resistant, corrosion-resistant material as the raw material of valve equipment, so that the valve has a longer service life, and cemented carbide is the best choice. Zhuzhou Chuangrui Cemented Carbide Co., Ltd. will share with you why integral sintered cemented carbide needs to be selected as a material for valves and pipeline equipment in the chemical industry.
In the coal chemical industry, mud and other material transportation pipelines, the sealing part of the valve is not only subject to the sliding friction and wear of the sealing auxiliary parts, but also to withstand the high-speed impact of the gas-solid duplex mixture with high temperature and high hardness, as well as the flashing and cavitation caused by high-pressure fluid, which leads to damage and aggravates the failure of the valve. Therefore, under severe working conditions such as powder transportation, wear resistance is a very important performance assessment index of the valve.
We choose integral sintered tungsten carbide as the material to make valve, which not only has high strength, but also has a high surface finish, when used other materials, the friction coefficient is smaller than steel, which can significantly reduce the friction of the contact surface and effectively reduce the operating torque
Integral sintered tungsten carbide is made by heating mixture of tungsten and carbon at high temperature, most of the tungsten carbide has high hardness,so it is not easy to decompose at high temperature, and also has good oxidation resistance.
In the coal gasification valve, the valve disc and valve seat are made of integral sintered tungsten carbide to form a sealing pair, and the valve has the following obvious advantages:
1、High hardness. hardness > 80HRC, which can withstand the high-speed erosion of multiphase particle media such as coal-water slurry, pulverized coal, silica fume, etc.
2、High temperature resistance. It can work at 750°C high temperature for a long time, and its strength, adhesion and thermal expansion are not limited by temperature, which fully meets the high temperature conditions such as coal chemical industry.
3、High pressure resistance. The transverse fracture strength of the overall sintered tungsten carbide can reach 4000MPa, which is more than 10 times of the conventional steel.
4、Corrosion-resistance. The overall sintered cemented carbide is chemically stable, insoluble in water even if heated, and does not interact with hydrochloric acid and sulfuric acid
5、Abrasion resistance. The characteristics of high hardness and high stability of the integral sintered cemented carbide ensure the excellent anti-wear performance of the sealing sub-material.
6、Erosion Resistance.
In general, the integral sintered tungsten carbide cemented carbide has high strength, high hardness, high melting point, high stability, low coefficient of friction, wear resistance, erosion resistance and cavitation, corrosion resistance, and the manufacture of wear-resistant valve seals for severe working conditions can greatly improve the applicability of the valve, expand the use range of the valve, and prolong the working life of the valve.
Zhuzhou Chuangrui Cemented Carbide Co., Ltd. provide high-end wear-resistant materials and professional valve surface hardening technology to provide solutions for the harsh working conditions of the coal chemical industry.
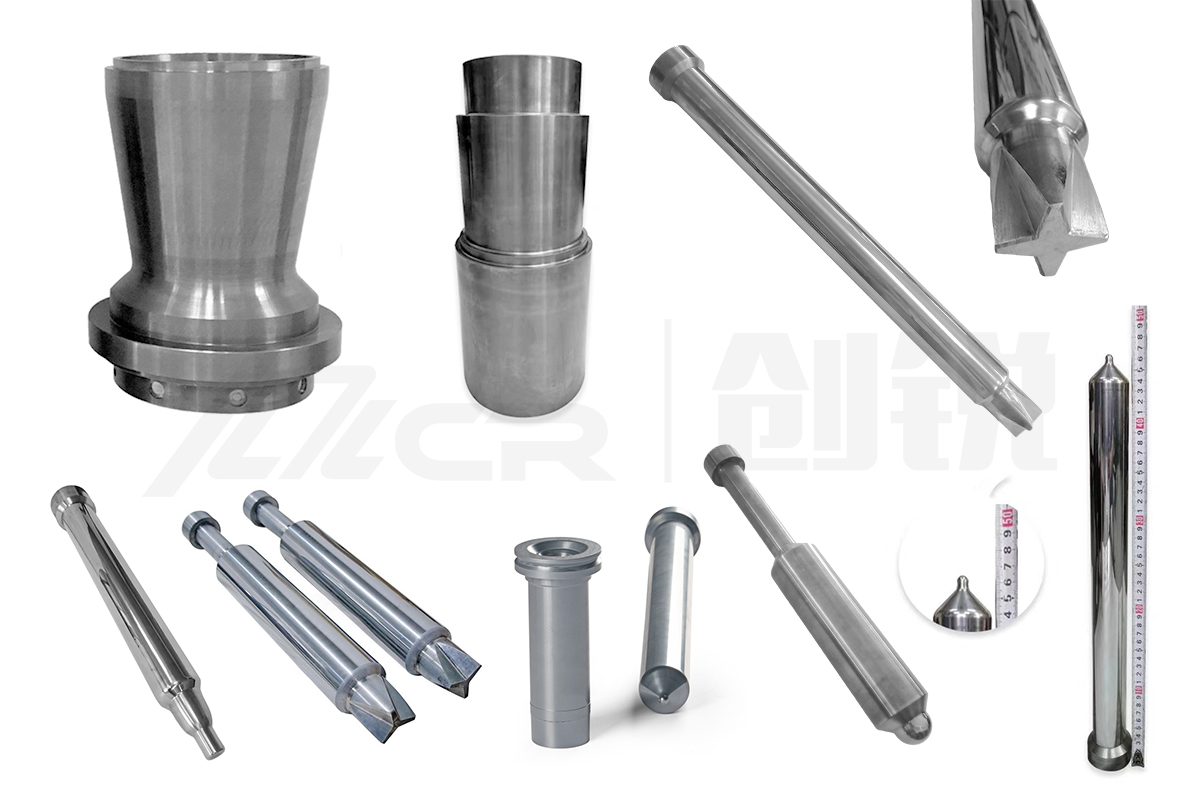
Post time: Jan-24-2024