Wear-Resisting Crushed Tungsten Carbide Grit,Grain And Granules Used In Oil Machinery
Description
Carbide broken grain is kinds of particles of hard alloy by cemented carbides broken method.Tungsten carbide grit’s particle size is 1mm~15mm different size.Can be customized different size product for customer requirement.It is used to welding or solder onto a steel body, to increase the wear resistance properties. For example, if a steel cutter can cut 24 hours without grits, it will cut 240 hours after with the tungsten carbide grits.
Tungsten carbide Grit containing rounded carbide particles offering superior wear protection, under conditions of low to moderate impact, through a combination of the inherent hardness of the Tungsten Carbide, and the “dead box” effect arise when particles of the abrasive material in contact with the hard facing are trapped between the carbide particles. This build-up causes “material on material” bulk flow, the base material thus being protected from abrasion damage.Tungsten carbide Grit is also supplied with sharp/blocky tungsten carbide grit for “cutting” applications where the excellent hardness of the tungsten carbide provides superior cutting performance.
• Cost Saving
• Less down time
• Reduced maintenance costs – Reduced replacement part costs
• Improved operating efficiency
The Physical Property of Tungsten Carbide Grit
Cobalt % | WC % | Hardness(HRA) | Density(g/cm3) | TRS(MPA) |
7-8% | 92%-93% | 89.5-90.5 | 14.6-14.85 | > 2500 |
Tungsten Carbide scraps is the material applied to components of applications with a high level of abrasion. It is applied as an overlay through a process called hard facing. Hard facing is a process in metalworking where tougher and harder material is applied to a base metal. Tungsten carbide grit is used above most traditional hard facing materials because it is harder and is proven to be a more effective protection against wear from abrasion.
Carbide broken grain can be created to suit individual applications and work environments. One can alter the grit mesh size as well as the wire matrix to achieve the desired balance of protection from abrasion and impact.Through hard facing, tungsten carbide grit can be applied to a new part in order to better its wear resistance or to a used part to restore its worn-down surface.
Carbide Grit is used for long lasting wear protection in areas of high abrasive wear. It is used to keep costly parts – bulldozer blades, wood grinding tips, trencher teeth, and bucket teeth – from wearing down quickly. Using tungsten carbide grit on machinery parts that see a lot of wear and tear significantly extends the life of those parts. For this reason it is used in many different applications including wood waste, agriculture, wear parts, plow attachments, and drilling. Grit adds an extra layer of protection to costly parts, increasing efficiency and decreasing downtime.
Production Equipment
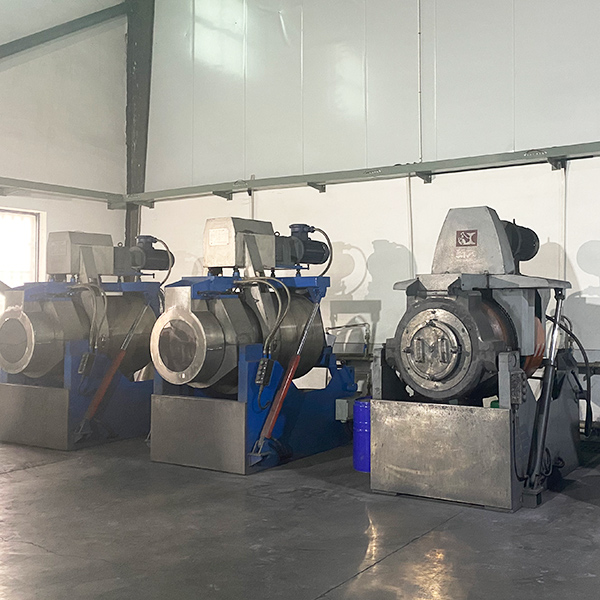
Wet Grinding
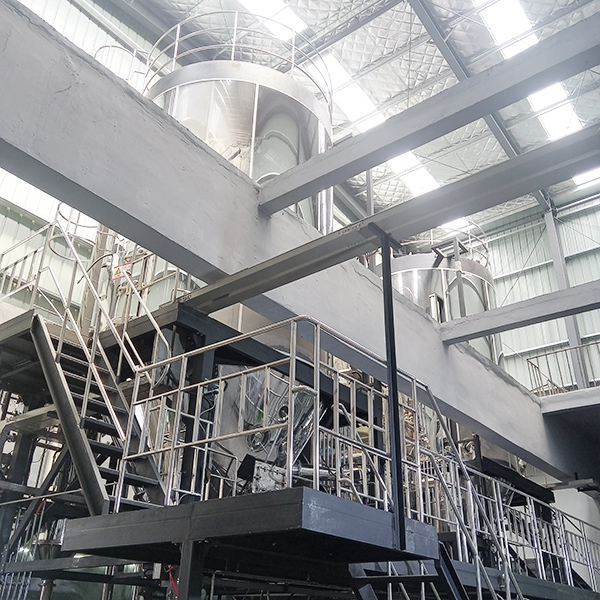
Spray Drying
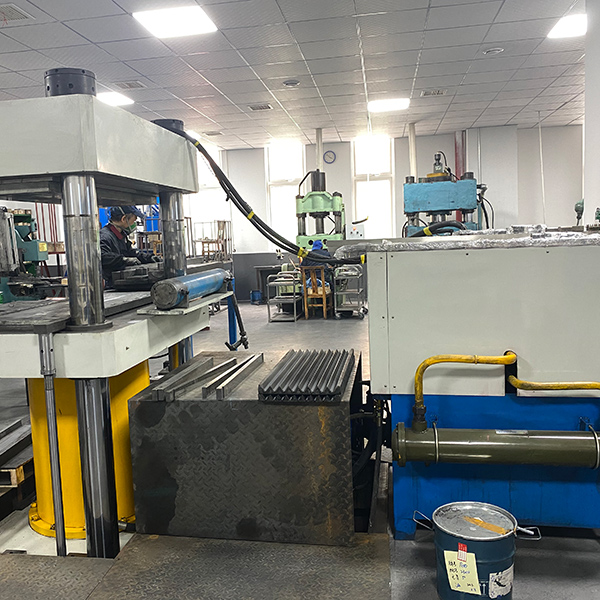
Press
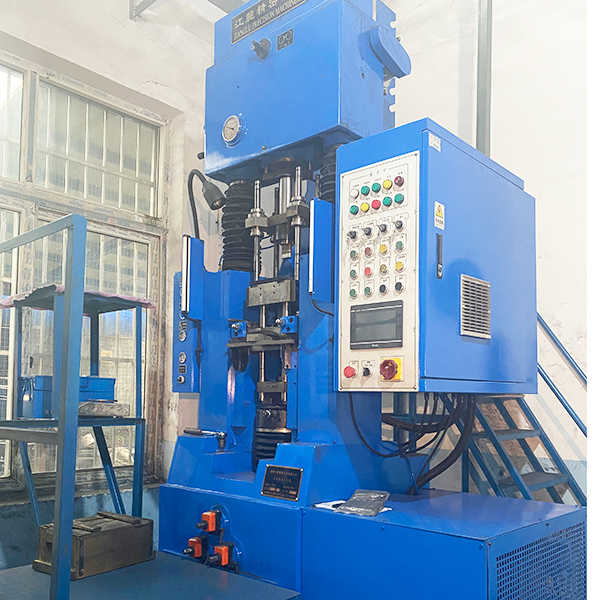
TPA Press
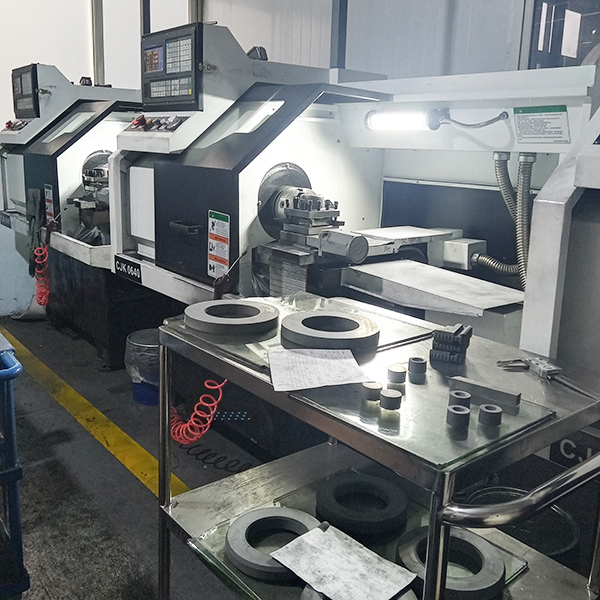
Semi-Press
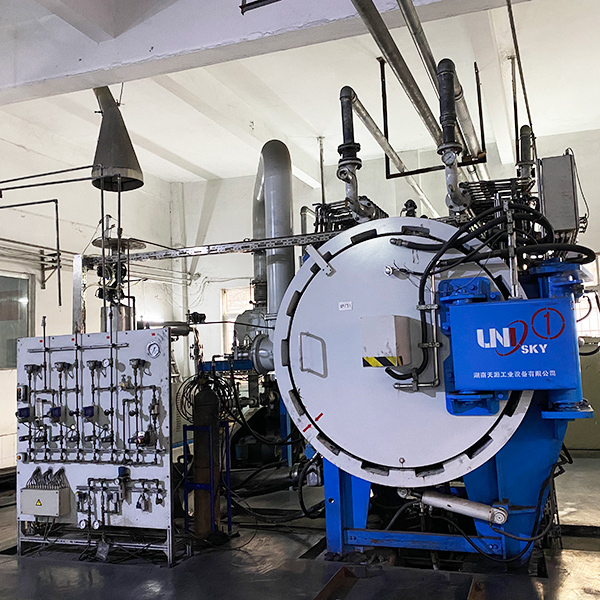
HIP Sintering
Processing Equipment
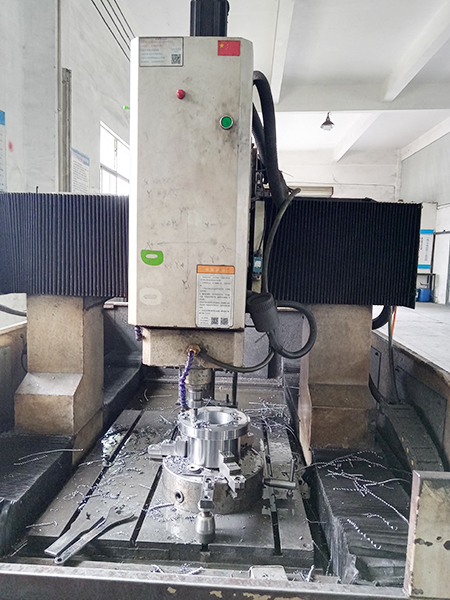
Drilling
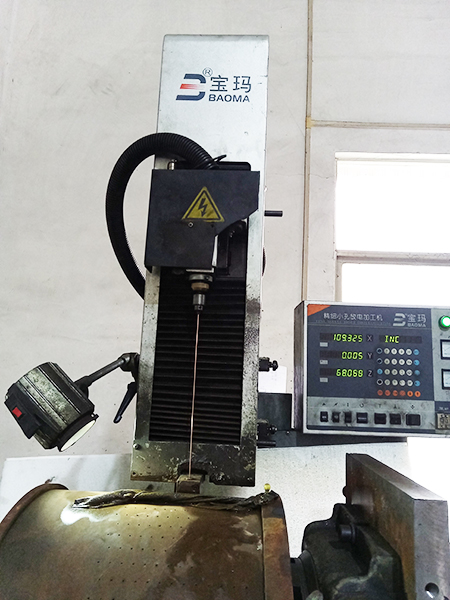
Wire Cutting
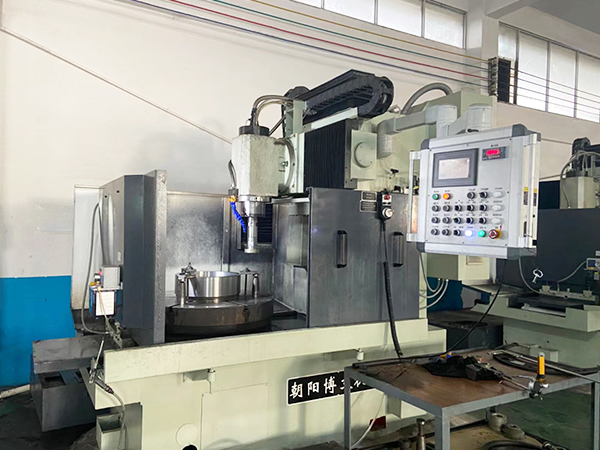
Vertical Grinding
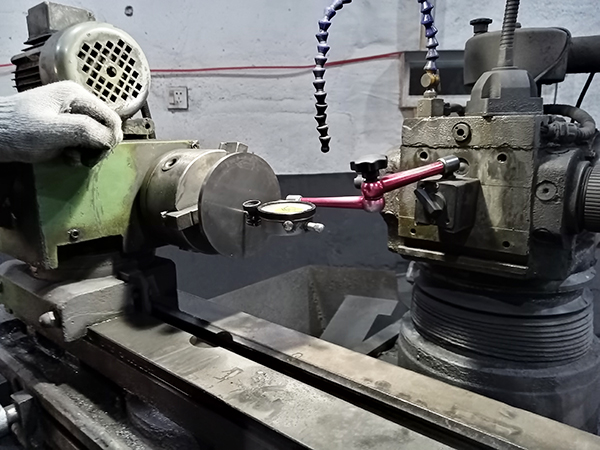
Universal Grinding
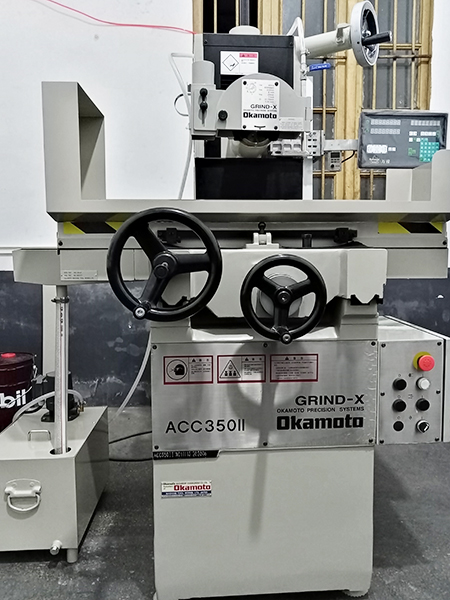
Plane Grinding
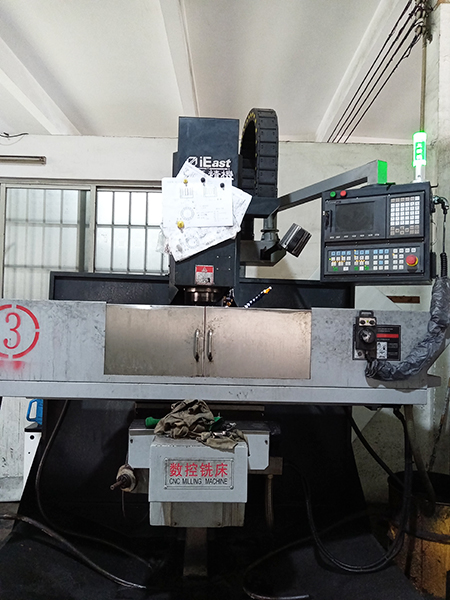
CNC Milling Machine
Inspection Instrument
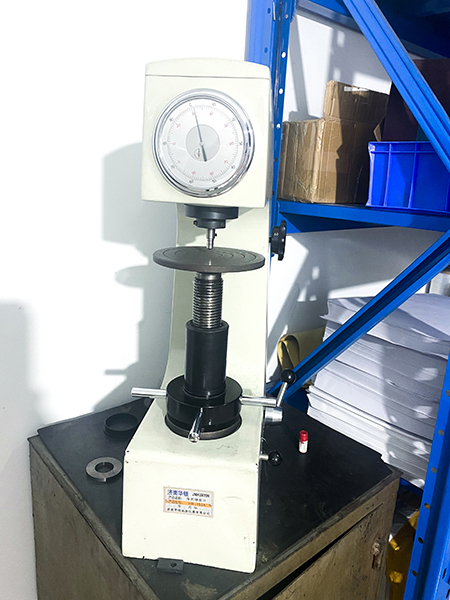
Hardness Meter
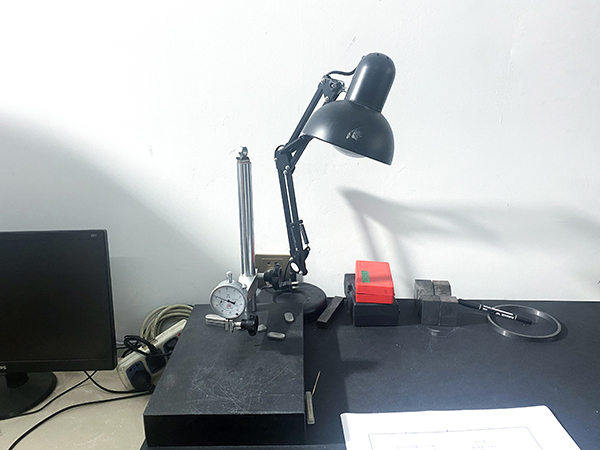
Planimeter
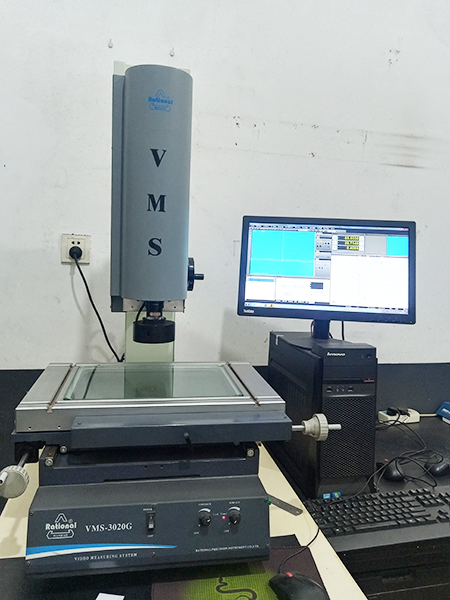
Quadratic Element Measurement
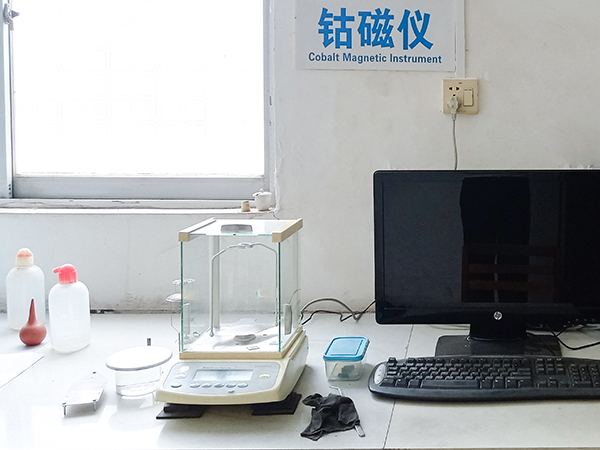
Cobalt Magnetic Instrument
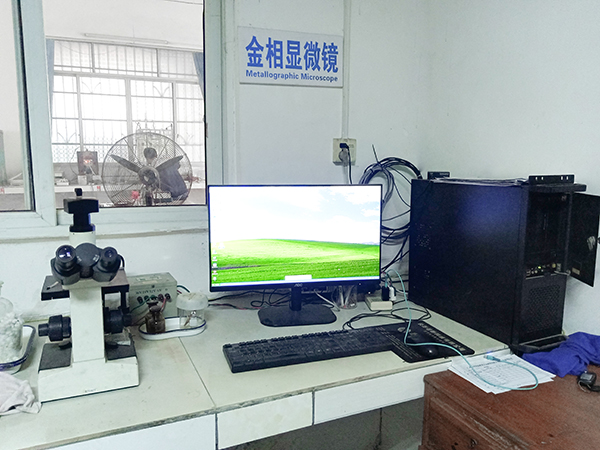
Metallographic Microscope
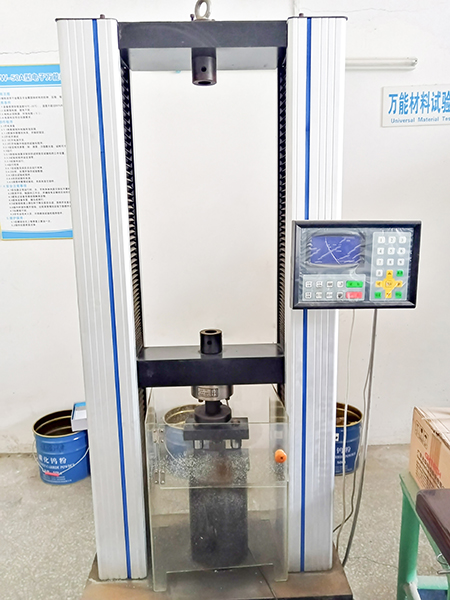